What is Roll Grooving?
- Share
- Issue Time
- Nov 24,2023
Summary
The blog discusses Roll Grooving as a connection method for industrial pipelines, detailing the process and materials involved. It emphasizes the purpose of grooved pipes in fire sprinkler systems and highlights the difference between Cut Groove and Roll Groove techniques. The article also explains how to roll a groove using the RG-1M on RIDGID 300 power drive.
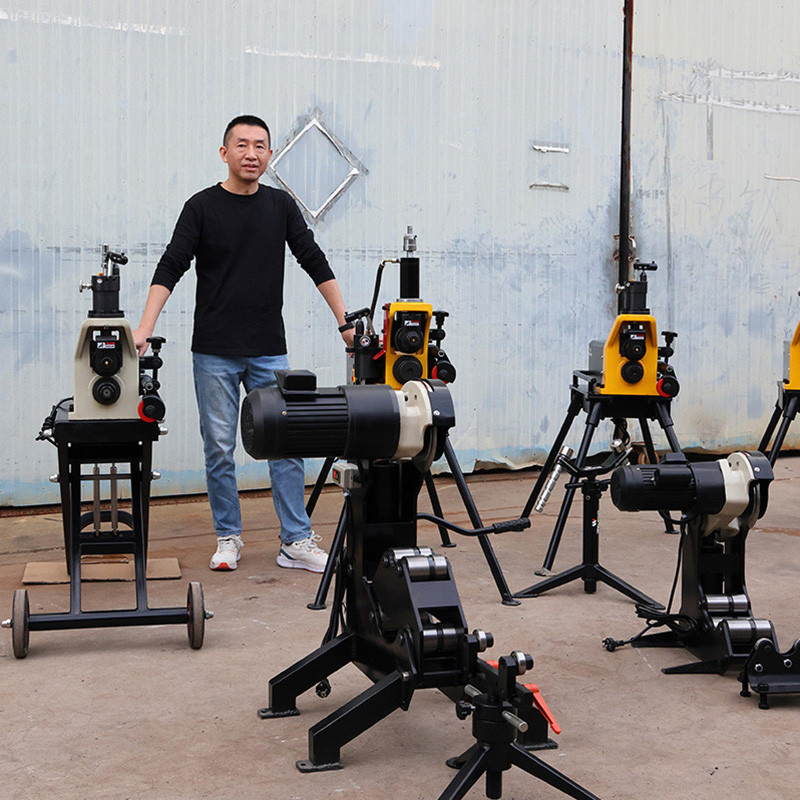
1.What is Roll Grooving?
The grooving process was developed in the mid-1950s and it has since emerged as a feasible connection method for industrial pipeline applications as opposed to welding and threading. Roll grooves were traditionally developed for light or thin-walled pipes. However, they are now used for a wide variety of pipe sizes and wall thicknesses without compromising the performance of the pipe joint or reducing the flow rate. The process works as follows: the pipe is placed on the drive wheel (the bottom wheel). Subsequently, the drive wheel makes the pipe rotate and the groove wheel (the upper wheel) grooves the pipe. The grooving process applies to copper, aluminum, steel, stainless steel, PVC and copper-nickel.
What is the Purpose of Grooved Pipes?
The installation of a fire sprinkler system consists of pipes. There is permanent water stored in these pipes which will automatically be released the moment the fire is detected. Because of the water stored in these pipes, there is a lot of pressure on them. Therefore, the pipes must be connected properly.
The grooves on both ends of two pipe ends could be joined together with a sprinkler coupling. The grooves in the pipe ensure that the pipes can be securely attached utilizing a sprinkler coupling.
2.What is the difference between the Cut Groove vs. Roll Groove?
When forming a roll groove, a pipe is cold formed to make a circular and extensive groove in the pipe. A groove is created without removing any pipe material. This is a new method compared to the cut groove, where pipe material is physically removed from the outside diameter of the pipe. Thereby, a groove is effectively cut into the pipe. Since no material is effectively removed with the roll groove, less waste remains than with a cut groove. Therefore, little cleaning work is required which subsequently speeds up the process of grooving pipes. Roll grooving can be applied on both heavy and light-walled pipes without weakening them against any corrosions. However, if the pipe wall is too thick, cut grooving the pipe will provide a more reliable groove.
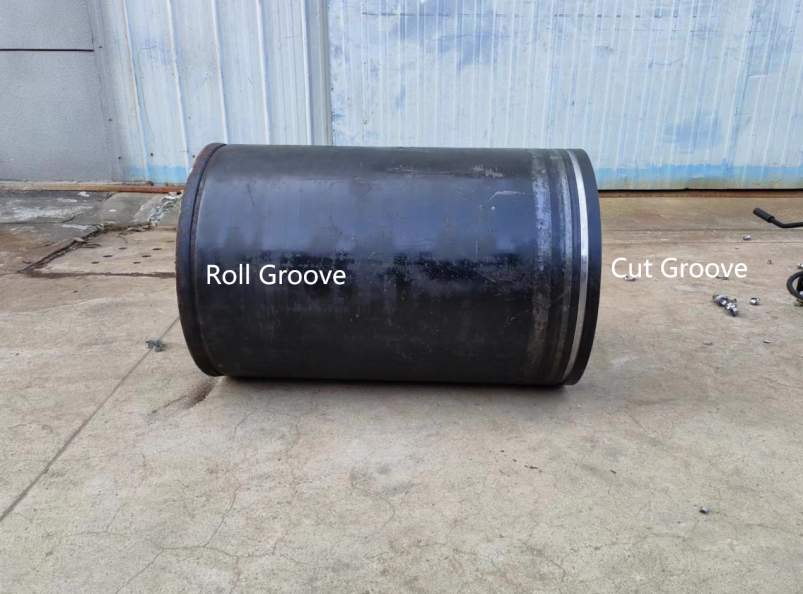
3.How to Roll a groove with RG-1M on RIDGID 300 power drive?
The Gruvmaster manual RG-1M roll groover mounts on the RIDGID 300 Power Drive for machine-powered roll grooving jobs, but is also designed to manually roll groove in-place pipe.
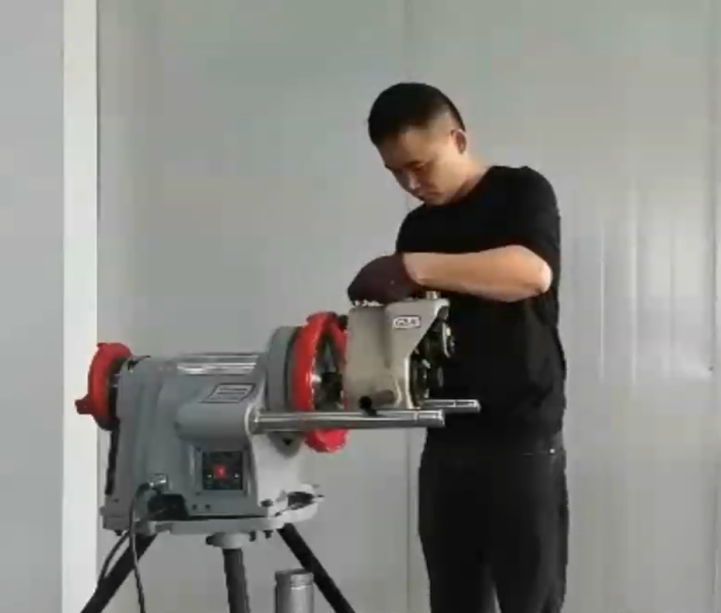
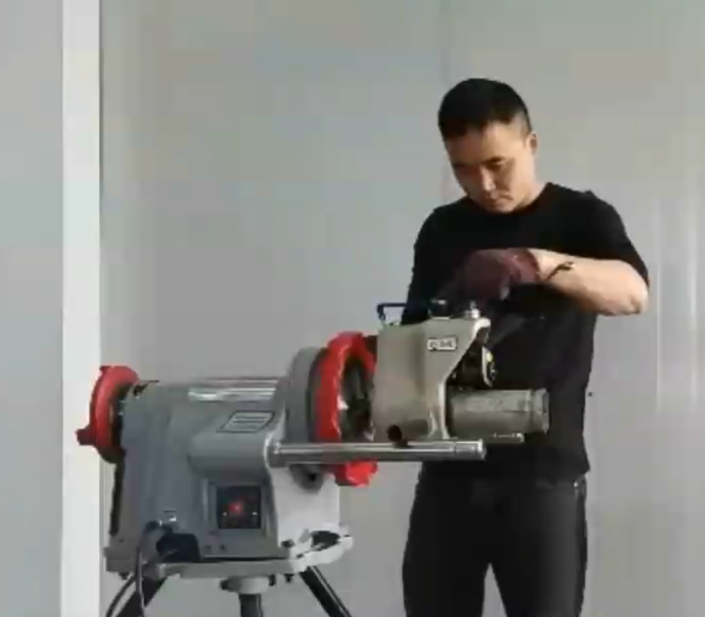
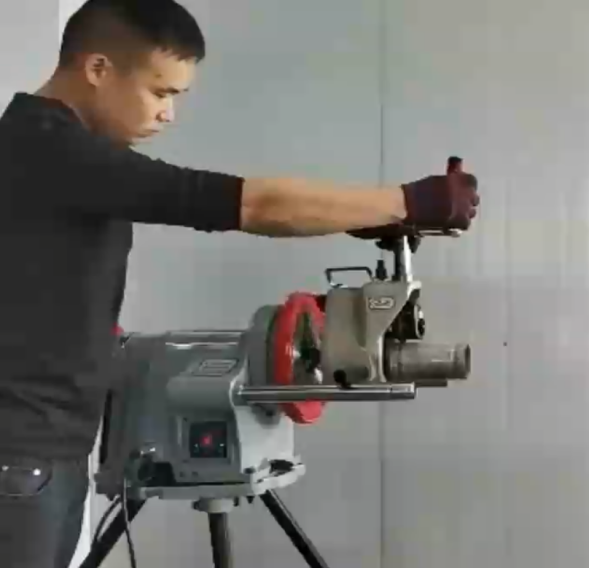
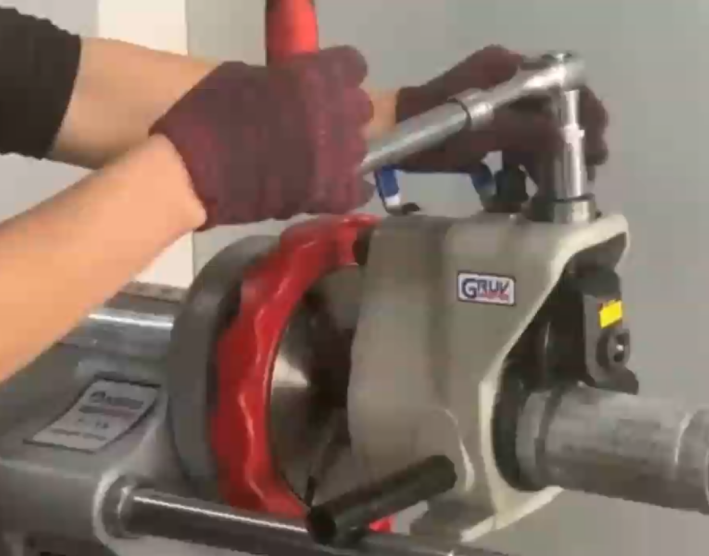
4. What is the difference between the Gruvmaster’s RG-2M manual roll groover and RIDGID 916 Power Driven Roll Groover?
Power-Driven 916 Roll Groover

The RIDGID Model 916 Roll Groover is the durable and efficient lightweight portable unit available. Built with a solid, durable cast-iron housing, it withstands heavy usage, yet is light enough for easy transportation.
While Gruvmaster’s RG-1M roll groover can be not only mounted on RIDGID 300 power drive easily,but also can be used manually. And the RG-2M is for 1”-6” steel pipes, SCH10 to SCH40

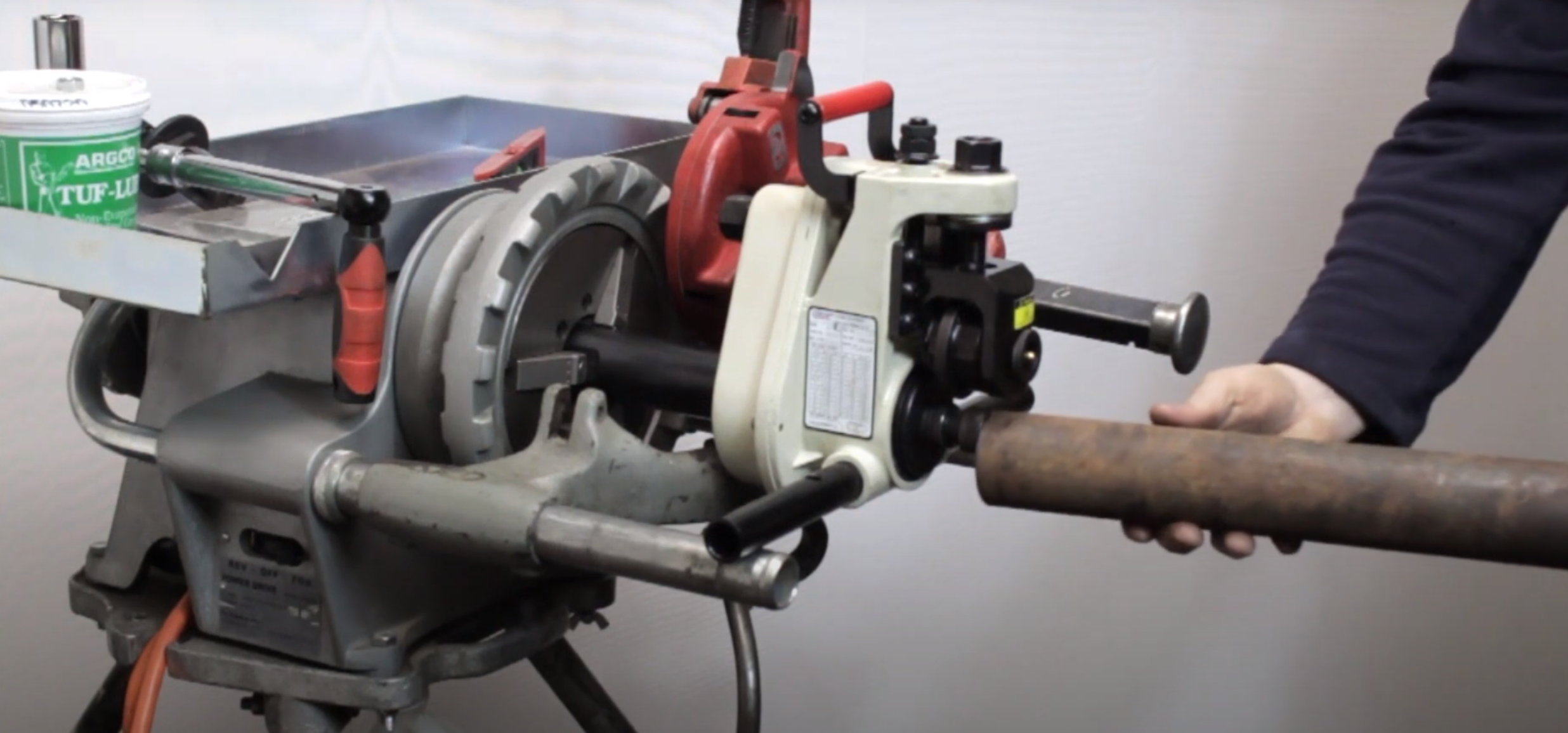
5.How to Groove a Pipe?
The fastest and easiest way is to use our Gruvmaster’s Roll Grooving Machine that can groove all pipe sizes sold by Welping. The pipe is placed on the pipe support and the knurl shaft causing it to rotate. Then, through hydraulic pressure, pinch roller is lowered on the pipe which creates the groove by cold forming. The process is done completely without heat and sparks.
See the following video and grooving machine user manual for a more detailed review of the process:
6.What is the difference between the Gruvmaster’s RG-2X roll grooving machines with Rothenberger ROGROVVER 1-12” ?
Through a simple comparison, Gruvmaster’s roll grooving machine can be used as a substitute of Rothenberger. Value for money
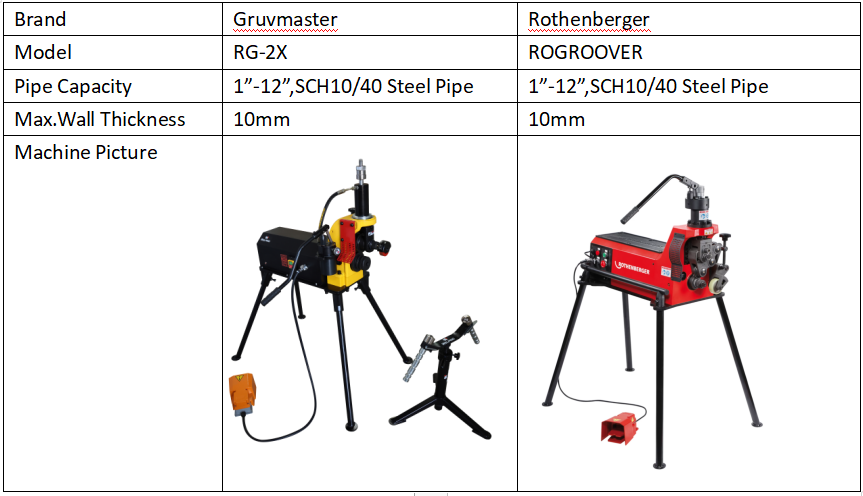